The logistics shed makes paperless management of load carriers a reality at FEGA & Schmitt
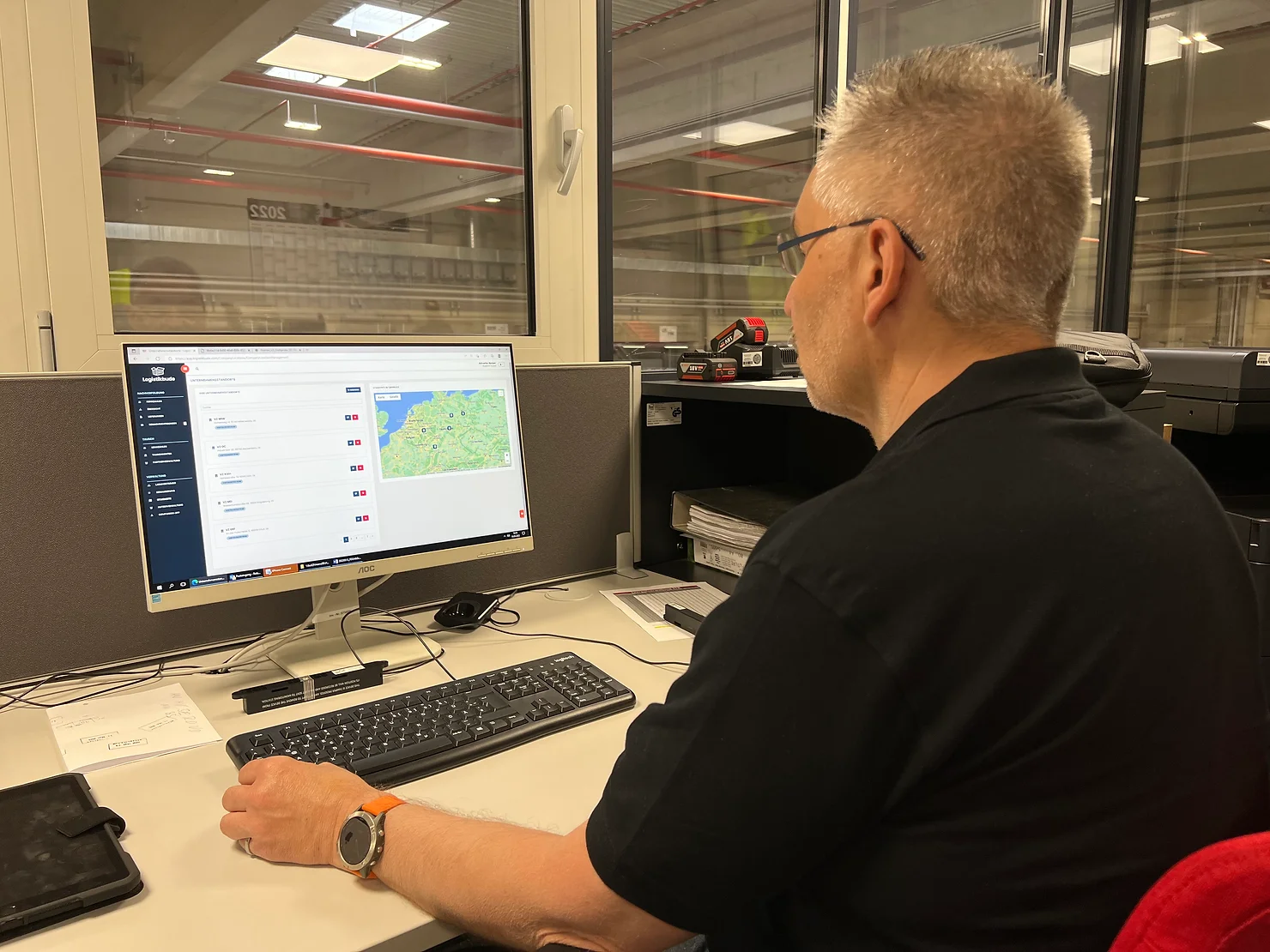
Who is FEGA & Schmitt?
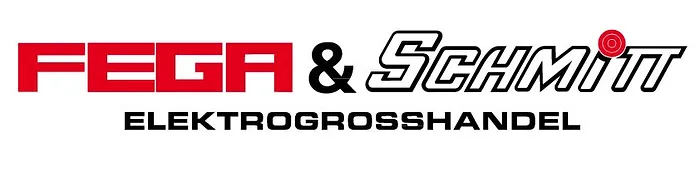
FEGA & Schmitt Elektrogroßhandel GmbH is a Würth company
group. With over 1,000 employees and 58 locations, FEGA & Schmitt is one of the leading electrical wholesalers in Central and Southern Germany. From the central warehouse in Heilsbronn, FEGA & Schmitt's distribution centers primarily supply industrial customers and craft businesses. The articles are shipped from the central warehouse on a wide variety of load carriers, from euro pallets to roll containers to small load carriers. Every day, various freight forwarders pick up the load units ready for shipment and bring them to the regional distribution centers, where the packages are then loaded into the vans and delivered.
How did the collaboration come about?
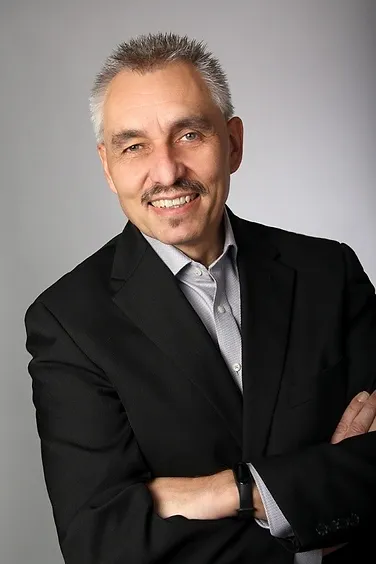
At a presentation of the Fraunhofer Silicon Economy research project, Roland Huber, Logistics Project Manager at FEGA & Schmitt, became aware of the spin-off “Logistikbude”. Initially, the intuitive tracking of already serialized load carriers was particularly exciting for Mr. Huber. After getting to know the team and the logistics shop solution, as well as testing the software independently, it became clear to him the power of the solution and further potential uses for digital load carrier exchange.
“I became aware of the founders of the logistics shop and their solution through an article in the magazine “Digitale Logistik”. The cooperation with the reasons, in particular with Michael Koscharnyj, is customer and performance-oriented. In the meantime, we are continuing our cooperation on an equal footing. ”
Roland Huber (Logistics Project Specialist at FEGA & Schmitt)
The numerous different reusable load carriers, which go from the central warehouse via freight forwarders to distribution centers every day, must be managed according to type, number and recipient and coordinated with each recipient regarding load carrier balances at the end of the month. As is usual in the industry, FEGA & Schmitt also documented exchange transactions on exchange notes and reconciliation of exchange accounts based on Excel.
Here, FEGA & Schmitt relied on the Logistikbude's innovative solution for digital exchange management. As a result, the entire exchange process in the central warehouse is to be carried out completely digitally — with the operative app, exchange processes in incoming and outgoing goods are documented and booked directly with appropriate exchange partners. Coordination with partners is no longer carried out periodically, but live via the logistics shop's web service.
“Real-time reconciliation enables us to correct incorrect entries immediately. Our diving partners now also appreciate this approach, who are also interested in further developing the logistics shed system and continuing to use the whole thing for their area management. ”
Roland Huber (Logistics Project Specialist at FEGA & Schmitt)
What did the joint implementation look like in practice?
The motivation for continuous improvement in internal processes paired with the openness to new technologies from Roland Huber's team at the Heilsbronn site has made joint implementation very easy.
After demonstrating the functions and on-boarding by the logistics shop team, FEGA & Schmitt took over the helm and set up the software according to their requirements. From the first test of the app to the creation of the users, the setting up of the accounts and the live delivery of the notification service, there was always a quick and open exchange between FEGA & Schmitt and the logistics shop. As a result, the purely digital exchange medium management for internal areas (in particular incoming and outgoing goods goods) and live account coordination with distribution centers and freight forwarders could be fully implemented in just a few weeks. During the implementation phase, Michael von Logistikbude accompanied the roll-out and was always available to answer any questions and requests from FEGA & Schmitt. In close cooperation, the central goals of paperless documentation of exchange transactions, increased transparency about exchange accounts and significant reduction in personnel costs for exchange account reconciliation for FEGA & Schmitt were achieved.
Since May of this year, digital exchange management with the logistics shed has been operational at FEGA & Schmitt.
“The added value is that we no longer make monthly statements, and there is also no need to enter charging certificates when using the app, which means that we can reduce administrative work here by 75%. ”
Roland Huber (Logistics Project Specialist at FEGA & Schmitt)
What's next?
Exchange management was just the beginning of the joint journey — the close exchange, the variety of ideas from FEGA & Schmitt and the wide range of functions of the logistics shed software still offer a great deal of potential for further use cases. In addition to the development of interfaces to the IT system and the IoT connection for high-quality load carriers, the next thing on the agenda is the tracking of serialized small load carriers (KLT) across the approximately 60 FEGA & Schmitts locations.
”Illustration of inventory management for load carriers at all locations. Algorithm to detect duplicate inputs. Tracking of reusable containers or any other means of loading with notification to the customer. Inventory overview of all distribution centers at a glance. Error messages via email for various applications after parameterization — just to name a few topics in future cooperation!”
Roland Huber (Logistics Project Specialist at FEGA & Schmitt)