What options are there to manage reusable use?
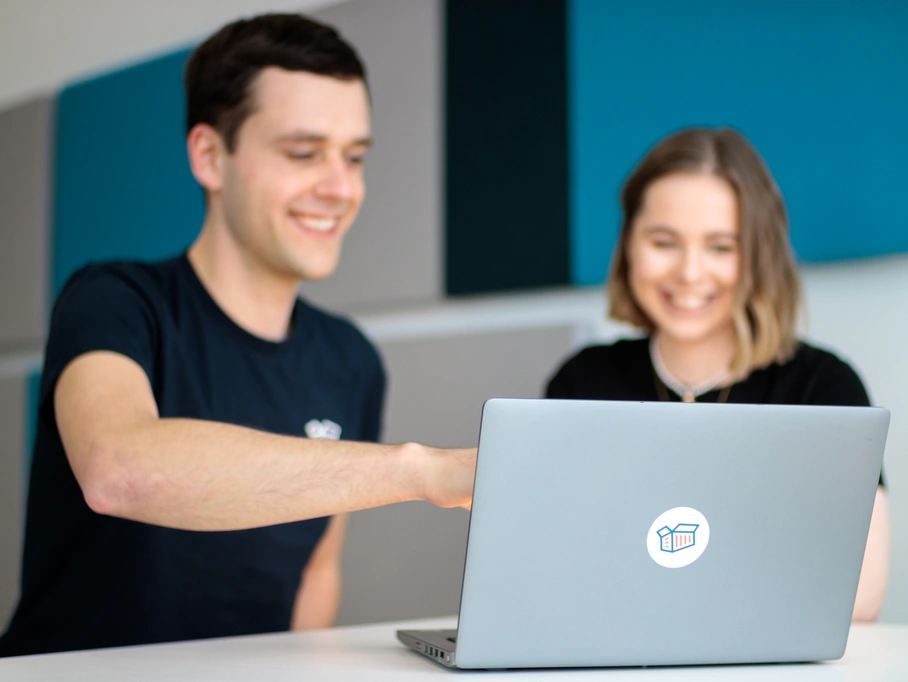
There are reusable properties in almost every company. First of all, classic logistical objects such as pallets, containers and mesh boxes come to mind. In addition, there are various other objects, from individual racks to special load carriers and swap bodies. And there are also reusable items away from logistics, e.g. in the form of food packaging, garbage containers or beverage crates. Because of this variety of very different objects, we always talk about “reusable objects” instead of load carriers, packaging, transport aids, etc.
Regardless of which type or combination of reusable objects a company has, there is always the question of management, i.e. how do I ensure that my existing reusable property is used as economically as possible. Economic means that both capital costs (inventory and repurchase) and personnel costs (documentation and coordination) are kept as low as possible. In the discussion, we find time and again that methods and technologies are often wildly mixed up. Therefore, in this blog post, we will first look at the basic methods for managing reusable use, before taking a closer look at the technologies and which of them fit which method.
Method 1: No method
The first method is actually not a method, but stands for the complete absence of the management of reusable objects. Many companies, particularly in the manufacturing sector, still treat themselves to this luxury. This goes so far that companies simply write off euro pallets as packaging costs. Even though the price is currently around 11.70 euros (see Pacurion News) is low in relation to the goods value of several thousand euros, this is a very good opportunity to save money immediately by switching to one of the following methods. In addition, this “method” must certainly be questioned in times of climate crisis and lack of resources.
Method 2: deposit
Probably the most widely used method for managing reusable use is deposit. It is used both between companies and in B2C and impresses with its simplicity and decentralization. If someone receives my reusable property, he or she pays a deposit and receives this back, partly reduced by a usage fee, upon return.
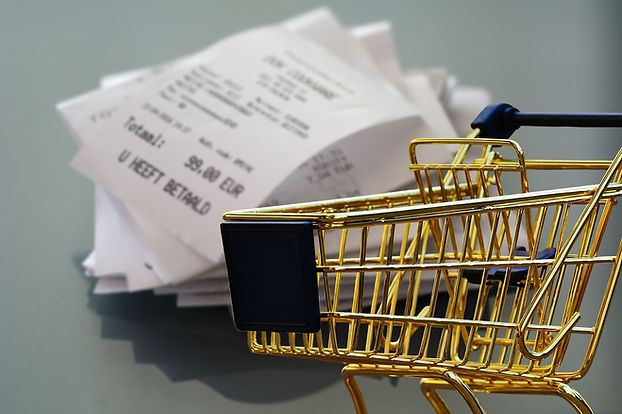
Each of us uses this method for beverage bottles in the private sector and many new concepts in the area of reusable food packaging are also based on it. Unfortunately, in practice, it has two decisive disadvantages that are often overlooked:
- In B2B, it doesn't work without booking
- The time component is neglected
Deposit works decentrally where payment can be made directly upon handover or payout upon return. This is the case in B2C, as payments are processed here at supermarket checkouts. In B2B, on the other hand, you first have to document the transitions between companies and then hand them over to the accounting department for a deposit statement. This requires a booking (= method 3) and an additional billing process.
The second disadvantage has to do with the deposit pricing model. This does not take into account the time component, i.e. it makes no difference whether I keep the reusable object for three days, three weeks or three months. This results in a significantly higher capital commitment, as the empties often collect until they are manually reclaimed or the storage space becomes too full. An effect that can also be easily observed with beer crates in summer, for example. The reusable material is therefore not used economically and you need significantly more properties, i.e. more capital commitment than actually necessary.
Method 3: Volume booking
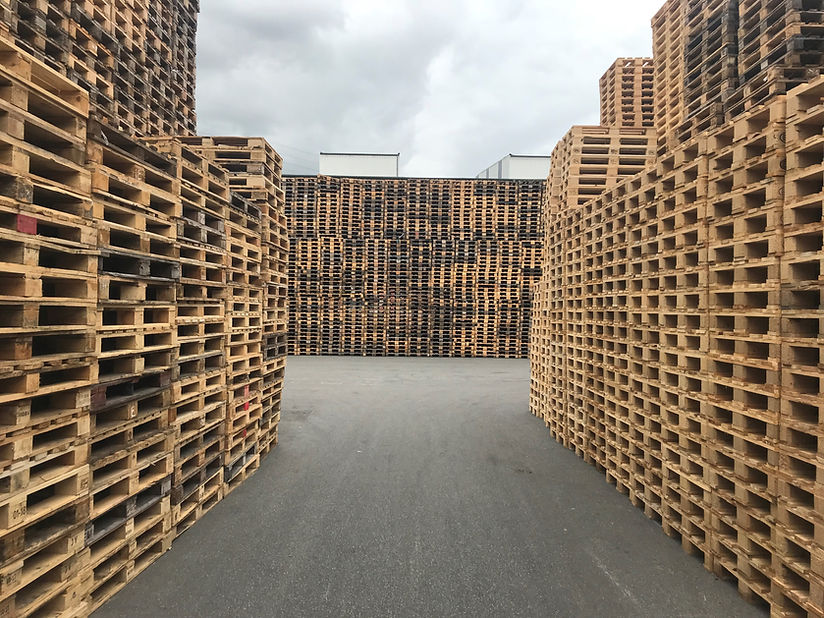
When posting quantities, reusable objects are posted as quantities as a result of a count. This makes it very easy to book large quantities, as only one number is entered. However, this method is prone to errors (a 3 quickly becomes an 8) and key figures such as circulation rate or shrinkage rates can only be estimated. The advantage is simple booking, which can also be made via interfaces to other systems, e.g. warehouse management system (WMS) or transport management system (TMS). For reusable objects from open pools, e.g. euro pallets or mesh boxes, this is the only method, as you never get back the same objects that you dropped off.
Method 4: Track & Trace
Unlike the previous method, Track & Trace clearly marks the reusable objects. A 1D or 2D barcode is usually used for this purpose. As a result, a state can be assigned to the object by means of a scan and the objects can be linked to further articles, as a result of which the load carrier becomes an information carrier. A status can also be set based on time, for example for annual testing or cleaning intervals. All states and scans are written into the digital file so that the history of each individual object is completely comprehensible.
In addition, the load carriers can be booked virtually with customers and suppliers without them having to scan. If the objects that are returned to the company's own company are scanned later, the turnaround time per partner can be automatically measured. This can then be used to implement automatic notifications (“You have already held this property 14 days, please send it back”) or to implement dynamic rental price models.
Method 5: IoT
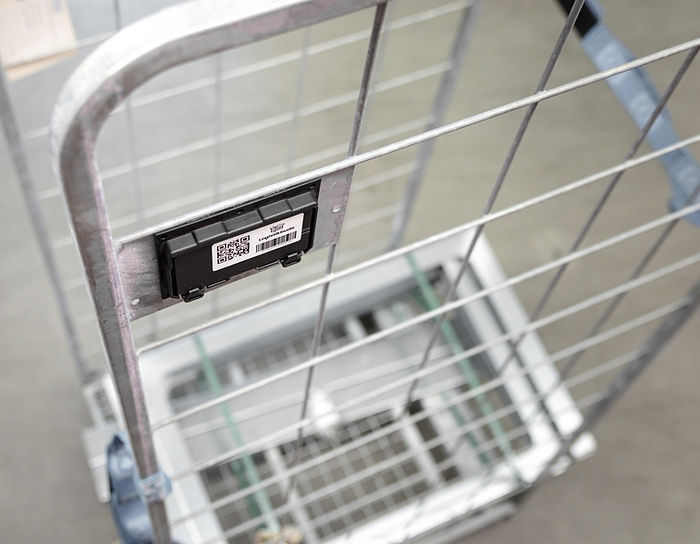
The fifth method involves attaching an IoT tracker to the reusable object. This eliminates the scan and allows the object to report itself. In addition to the unique number, the current location and other data, such as movement profile or temperature, are also transmitted. This transfer is usually carried out in data packets, i.e. the recordings of the last minutes or hours are combined and transmitted in an event to save energy. The disadvantage of this method is the high price per IoT tracker. Together with the usage fee for the mobile network, this is 3-4 euros per month.
Which method do I use now and when?
Finally, there is, of course, the question of which method should be used and when. First of all, there are reusable objects in open pools that cannot be changed (economically) because you never get the same objects back. Here, you are therefore dependent on the pool operator to apply a barcode or even IoT. If this is not the case, it is recommended to book quantities here from an ecological and economic point of view. We have learned from the implementations carried out by our customers that the value of the reusable property is often a good indicator for the choice of method:
- 0 to 30 euros: volume booking
- 30 to 500 euros: Track & Trace
- Starting at 500 euros: IoT
These are only rough guidelines, which may also vary depending on the use case. In addition to the value of the objects, the value of the transported articles also plays an important role. In the pharmaceutical sector, for example, it can be useful to use an IoT tracker with a temperature sensor even if the value of the object is low. After taking a detailed look at the methods for managing reusable materials in this blog post, the next post will be about different technologies and how they fit into the individual methods.