Collaboration with Logistikbude: ims reduces tool shrinkage by up to 50 percent
.webp)
The tool rental company ims GmbH from Hünxe uses the software solution from Logistikbude GmbH to manage its loaned tools - with complete success. This enables its customers to significantly reduce tool shrinkage on their large construction sites and thus also shrinkage costs by up to 50 percent. At the same time, the administrative work involved in reordering materials is reduced for both sides. ims is now aiming to offer the logistics centre as an exclusive additional service to all its partners.
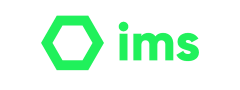
ims GmbH is a leading lessor of industrial tools and tool solutions. ims has particular expertise in providing tool support for national and international turnarounds; with tool and container solutions specially designed for turnarounds, ims offers customers targeted support for their time and resource-critical tasks. The ims group of companies also offers associated services from a single source and with reliably high quality. These include, for example, downtime-specific consumables or the realisation of time-critical transports.
A large proportion of its customers are service providers who carry out time-critical maintenance or repair work for large industrial companies. The contractors' main projects are so-called turnarounds, in which entire industrial and petrochemical plants are completely shut down for maintenance work. In order to minimise plant downtime and the associated loss of revenue, several thousand specialists work on site at peak times. Within a few weeks, they shut down the plant partially or even completely, maintain and repair it and then reassemble it. As a tool supplier, ims is an important link in this time-critical and volatile chain.
All-round carefree package for time-critical repair work
‘We are commissioned to put together the equipment required on site. This actually includes everything - from angle grinders and personal protective equipment to large welding machines. We deliver the all-round carefree package so that the service providers on site can concentrate fully on the maintenance work,’ says Ole Sörensen, Commercial Manager of the ims site in Mainhausen. To do this, the ‘tool all-rounder’ loads entire containers with tools and delivers them directly to the construction site, where the warehouse staff then take care of issuing them. Once the turnaround is complete, ims collects the container again and checks the stock of tools when the goods are returned.
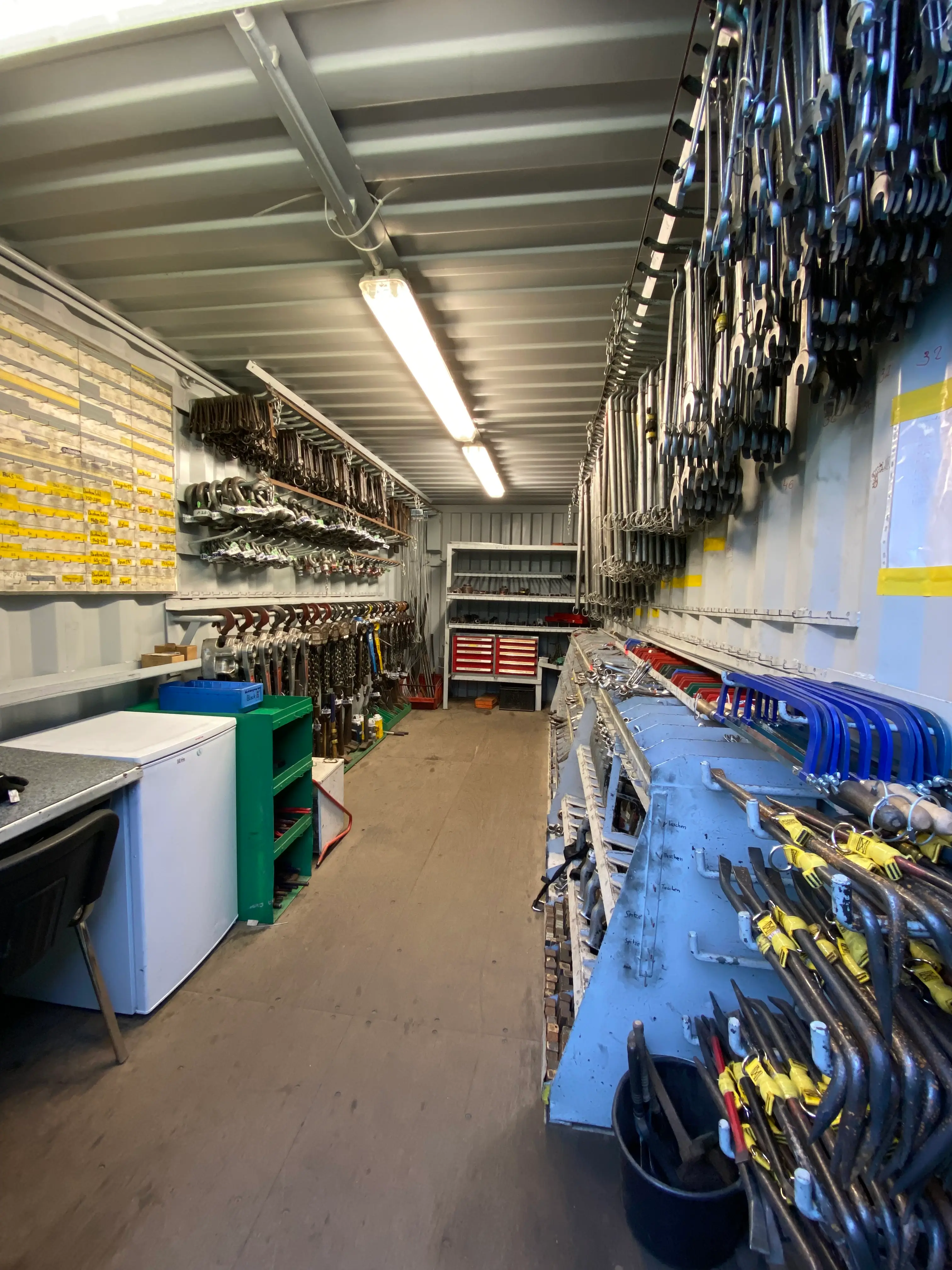
Tool shrinkage with high costs
In the past, the team often had to realise that Significantly fewer tools were returned than were delivered. David Skowasch, responsible for strategic purchasing and project management at ims, reports: ‘The loss of tools was a major problem for us and our customers: Significant quantities of tools were not returned for major projects.’ This loss of tools causes high costs for ims and its customers and a high administrative burden on both sides: The tool supplier has to coordinate with the contractors and compensate for the losses. ‘We don't earn any money by charging our customers for the lost items and ordering new tools - on the contrary. These are efforts and costs that we are happy to avoid,’ says the site manager. His and his team's top priority is to reduce tool wastage, save costs and gain productive working time.
Digitisation of analogue documentation
At the same time, the documentation for tool dispensing was also to be digitised in order to improve traceability - this had long been a thorn in the side of David Skowasch's team. ‘Until now, the tool issue documentation was analogue. At the end of a turnaround, we ended up with five to six folders filled to the brim with output slips,’ explains Skowasch. The problem: the manual documentation made it time-consuming to process the lost items.
User-friendliness as a predictor of success
In response to the loss of tools and complex documentation, the ims team was looking for an intuitive software solution for tool management. ‘Logical and simple operation was the most important thing for us, as the software is used by our customers for time-critical projects such as turnarounds - and there is no time for lengthy familiarisation,’ says Skowasch. For this reason, the group of companies had to stick to written documentation for a long time - complicated software solutions would not be used in the hectic day-to-day work. ‘Even the best tool can only help if it is actually used,’ Skowasch knows from practical experience. His team found what they were looking for at Logistikbude.
Intuitive and fast booking
The ‘Bude’ is a start-up from Dortmund and digitises the management of loading aids, i.e. pallets, pallet cages or racks, with its software solution of the same name. It is most frequently used in the supply chain by shippers, logistics service providers and retailers, but it also covers the requirements of tool hire companies perfectly. The software is designed to work quickly and reliably - even under hectic conditions. It enables the tool all-rounder to enter site-specific tools, including article numbers, into a database and thus digitally map the inventory of a tool container. All products are stored in the logistics centre database with their own serial numbers. If a worker needs a cordless impact wrench, the magazine operator uses the application to scan its serial number and assign it to the construction worker. Thanks to the logistics centre, site managers can keep track in real time of which tools have been issued and when, and whether they have been returned. As soon as the cordless impact wrench is returned, the booking process can be completed with a scan.
‘When we used Logistikbude as part of a pilot project, we asked ourselves whether our customer was actually using the software because, surprisingly, there were no queries. That's the ideal situation when you use new tools - they are self-explanatory,’ says Skowasch.
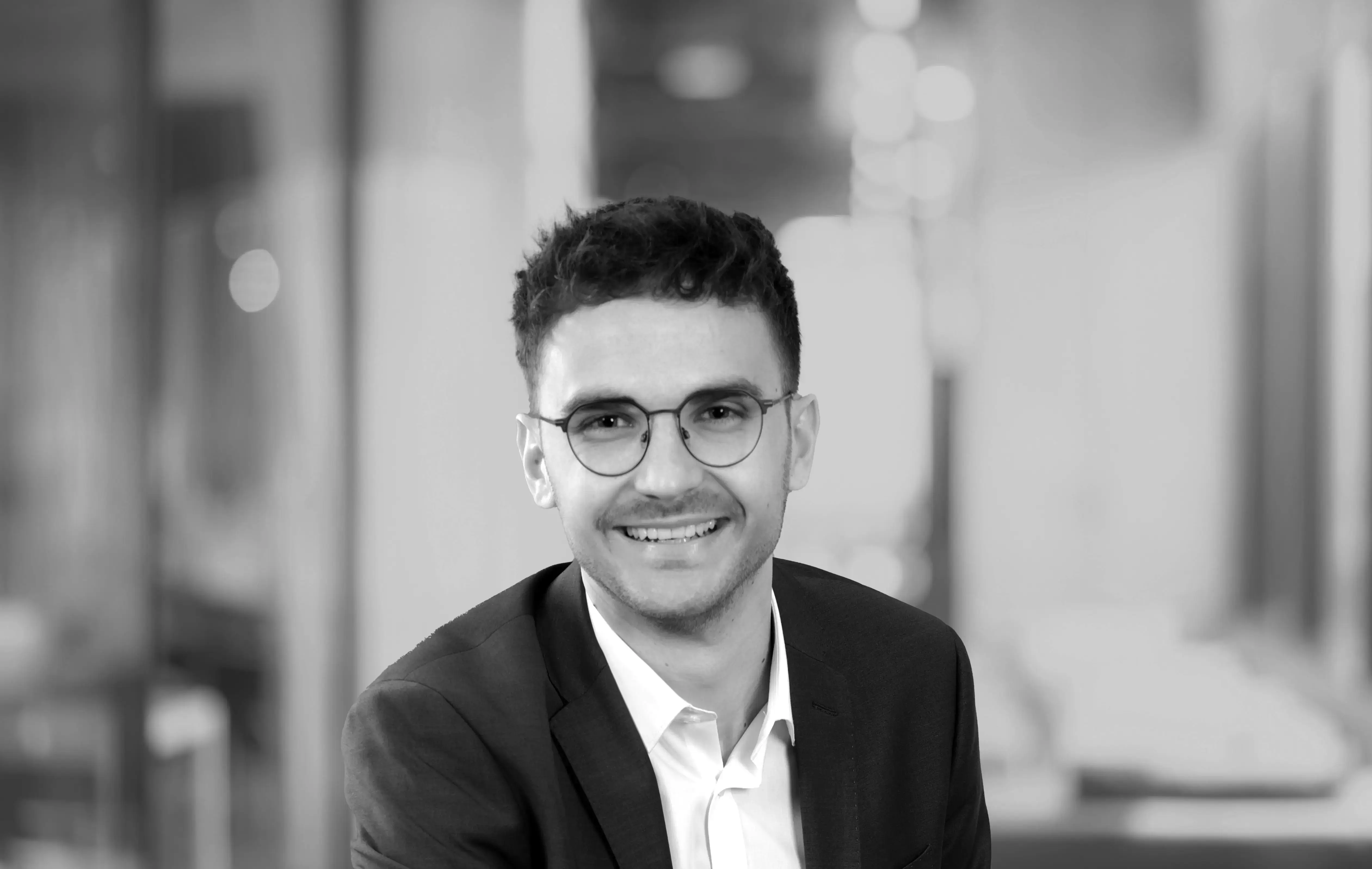
Significantly reduce material wastage and administrative costs
The first return of goods after implementation of the logistics centre is striking: Tool shrinkage is significantly reduced. The resulting costs can be reduced by up to 50 per cent thanks to the software solution.
Sörensen says: ‘This is a win-win situation for us and our customers. They save on shrinkage costs and both sides can also reduce their administrative expenses thanks to the lower loss items.’
This shows that the effects that Logistikbude achieves in the management of loading aids - a lower repurchase rate with less administrative effort - can also be transferred to tool hire. In both cases, Logistikbude achieves this through an improved overview, a simple workflow and real-time tracking. In addition, ims has observed a further effect that the logistics hut has achieved in everyday working life: ‘The improved traceability also sensitises the employees on site: they handle the tools more carefully,’ says the commercial site manager.
Expansion of cooperation planned
These effects also impress ims' customers. ‘Everyone I showed the solution to was enthusiastic about the software. If there is software that not only reduces shrinkage costs but is also easy to use, then that is attractive for the contractors,’ reports Sörensen. For this reason, the tool all-rounder is planning to further expand its collaboration with Logistikbude. Sörensen: ‘Our aim is to offer the logistics centre as an exclusive additional service.’

Excellent feedback for the start-up. Fabian Bahnsen, Head of Sales at Logistikbude, says: ‘Although Logistikbude was originally designed for load carrier management - and this remains our speciality - our cooperation with ims demonstrates the flexibility of our software and our team.’
Schedule a free consultation now!
We would like to get to know you and your current challenges with reusable objects. As a first step, we analyse your status quo together and check where there is potential for optimization and automation. If we have a suitable solution for you, we will present our solution to you on your use case in a second appointment.